You quoted the part. The customer placed the order. Seems like everything went smoothly — until production flags a problem.
Now you’re sending awkward emails about design changes, delays, or extra costs. Nobody likes that moment — and it’s avoidable.
That’s where automated DFM feedback comes in.
Because the best way to fix a manufacturing issue… is to catch it before it happens.
And with the right quoting software, it’s easier than you think.
🧠 What Is DFM — and Why It Matters to Customers
DFM (Design for Manufacturability) ensures that the parts your customers submit can be produced smoothly — with realistic machine capabilities and pricing that protects your margins.
In many job shops, custom fabrication businesses, or metal parts manufacturers, quotes are still built manually, often based on incomplete CAD file review or flat-rate templates.
That leads to underpriced quotes, rushed reworks, and lost trust.
💬 Customers May Not Ask for It — But They Notice It
Most customers don’t say, “Please validate my part.”
But they do notice when you:
- Catch a problem before it hits production
- Flag risky features like unsupported threads or thin walls
- Provide feedback instantly, even via your online quoting system
- Avoid production delays by adjusting expectations early
Even when they don’t say thank you — they remember it.
That’s what builds confidence in your manufacturing services.
🔍 How Digifabster Catches Problems Early
Digifabster uses real-time feature recognition and DFM analysis to review uploaded 3D models and CAD files before a quote is shown.
The system automatically detects:
- Critical features: holes, threads, pockets, thin walls, undercuts
- Unusual geometries that affect machinability
- Models that exceed your machine’s envelope or violate rules
- Files with missing info or complexity too high for standard quoting
This turns your quoting process into a proactive cost estimator — not just a calculator.
⚙️ DFM Rules That Fit Your Shop
You can customize DFM logic to reflect the real-world limits of your operation — whether you’re focused on CNC machining, sheet metal, 3D printing, or prototype manufacturing.
Use Digifabster to:
- Set rules per machine or material
- Trigger TBD Mode when unsupported features are detected
- Send custom messages for flagged parts inside the quoting interface
- Hold quotes for review on high-risk geometries or high-value jobs
It’s a smarter way to blend automation with your internal standards — without adding friction.
🙌 Less Friction. Fewer Surprises. Happier Customers.
When DFM feedback is built into your quoting workflow, everyone wins.
- Your team avoids rushed corrections and bad surprises
- Your customers trust your pricing and professionalism
- You build repeat business through better ordering experience
- And your quotes stay accurate — even as complexity increases
For small machine shops and scaling on-demand manufacturers, it’s one of the easiest ways to stand out.
✅ Final Thought
Customers won’t always say “thank you” for catching a design issue.
But they’ll remember the shop that helped them avoid a mistake.
With Digifabster’s built-in DFM analysis, feature recognition, and automated quoting tool, you quote faster — and smarter.
Ready for the switch?
Learn more about Digifabster’s instant quoting, order management, invoicing, and payment solution here.
YOUR PATH FORWARD STARTS TODAY
Start your free trial now. No sales call required.
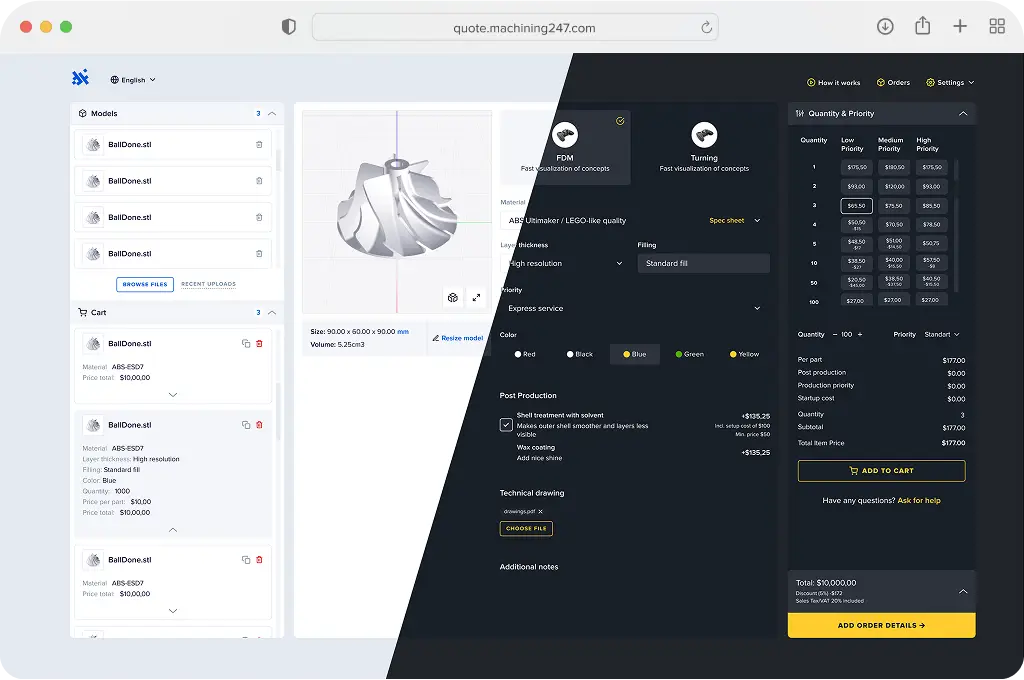