Maximize material usage and quote smarter — with one click.
DigiFabster’s Nesting feature for laser cutting and sheet metal fabrication analyzes your part geometry and orientation to fit as many parts as possible onto a single sheet. This helps optimize raw material usage, reduce scrap, and improve production efficiency — especially for high-volume or multi-part jobs.
It’s a powerful tool for fabrication shops, metal parts manufacturers, and any machine shop quoting sheet metal work or laser cutting services.
🔧 What It Does
With Nesting, you can:
- Analyze all parts in an order and automatically nest them for optimal layout
- Fit multiple part copies onto a single sheet of material based on:
- Part geometry
- Orientation
- Sheet size
- Reduce waste and calculate material cost more accurately
- Use the nested file output to inform more efficient cost estimation and job planning
Nested layouts can be generated and applied with just one click — giving you better insights into the true material and time cost of an order.
🏭 Problems This Solves
Problem: Material usage is hard to estimate accurately
✅ Solution: Nesting provides a realistic layout so you can see how many parts fit on each sheet — improving your quoting software accuracy.
Problem: Manual nesting wastes time and leaves room for error
✅ Solution: Automate the process and apply nesting in seconds, helping your estimating software and workflow automation tools work smarter.
Problem: Material waste increases job cost unnecessarily
✅ Solution: Nesting reduces scrap and supports cost reduction strategies in metal fabrication and sheet metal work.
🚀 How It Works
- Go to the Order Details page
- Click “Apply Nesting”
- The system analyzes all laser-cut or sheet metal parts in the order
- A nested file is created and saved with the order for download or reference
You can then use this file for quicker quoting, material purchasing, or production planning.
💡 Pro Tip
Use nesting early in the quoting phase to improve the accuracy of large or multi-part jobs. This is especially helpful when dealing with high-volume aluminum fabrication, stainless steel parts, or custom sheet metal components — where even small optimizations can save big on cost and material.
YOUR PATH FORWARD STARTS TODAY
Start your free trial now. No sales call required.
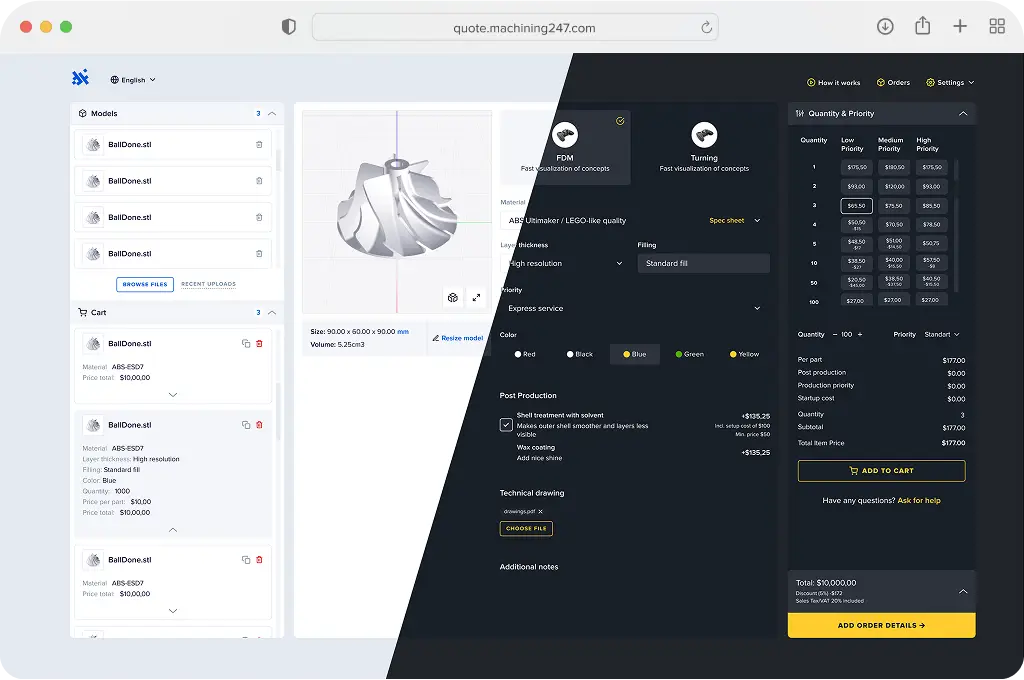