Make it easy for your customers to configure and order parts — without a single email.
DigiFabster’s Online Storefront gives your customers an intuitive, e-commerce-style interface where they can fully define their parts before placing an order. From material selection to post-processing, colors, and tolerances, the entire process is streamlined for speed and simplicity.
Ideal for CNC machining, 3D printing, sheet metal fabrication, and custom manufacturing workflows — this feature enhances customer satisfaction and reduces quoting errors.
🔧 What It Does
After uploading a CAD file, your customer can:
- Select:
- Material type (aluminum, steel, plastics, etc.)
- Manufacturing process (e.g. CNC milling, laser cutting, 3D printing, injection molding)
- Post-processing options (anodizing, polishing, heat treating, etc.)
- Colors (if supported)
- Surface finish and tolerances
- Quantity and delivery preferences
- Automatically detect part features and run DFM (Design for Manufacturability) checks:
- Analyze geometry in real time
- Assess manufacturability based on selected materials and processes
- Identify potential design issues like:
- Thin or unsupported walls (via wall thickness checks)
- Non-manufacturable features
- Overly complex geometry
- Ensure accurate pricing and reduce risk of production errors
- See instant price updates based on selections (when pricing is automated)
- Submit orders confidently, with clearly displayed specs and visual feedback via the 3D CAD File Viewer
This reduces friction in the manufacturing workflow, builds customer trust, and increases quote-to-order conversion rates.
🏭 Problems This Solves
Problem: Customers don’t know how to submit complete RFQs
✅ Solution: A clean, step-by-step configurator guides them through everything — from model upload to final quote.
Problem: Sales teams spend time clarifying incomplete quote requests
✅ Solution: Orders come in with all specs defined — no more chasing material type, color, or tolerance data.
Problem: Quoted parts aren’t always manufacturable
✅ Solution: Built-in DFM checks, including wall thickness validation, ensure designs match your shop’s real capabilities.
Problem: Online ordering feels clunky or outdated
✅ Solution: This modern, e-commerce-style interface improves the buying experience, especially for repeat customers or tech-savvy buyers.
🚀 How It Works
- It works out of the box
– Configuration is integrated directly into your quoting widget or secure standalone solution - Customer uploads a CAD file
– Immediately enters the part configurator interface - They select all options step-by-step
– Material, process, post-processing, color, tolerances, quantity, and more - DFM runs automatically
– Flags manufacturability issues like thin walls, unsupported features, or oversize geometry - Order is submitted with full specs attached
– You receive accurate, optimized job data
💡 Pro Tip
Use DFM flags and wall thickness thresholds to trigger manual review mode for parts that need special attention — ideal for jobs involving 3D printing, metal bending, or fine tolerance machining.
YOUR PATH FORWARD STARTS TODAY
Start your free trial now. No sales call required.
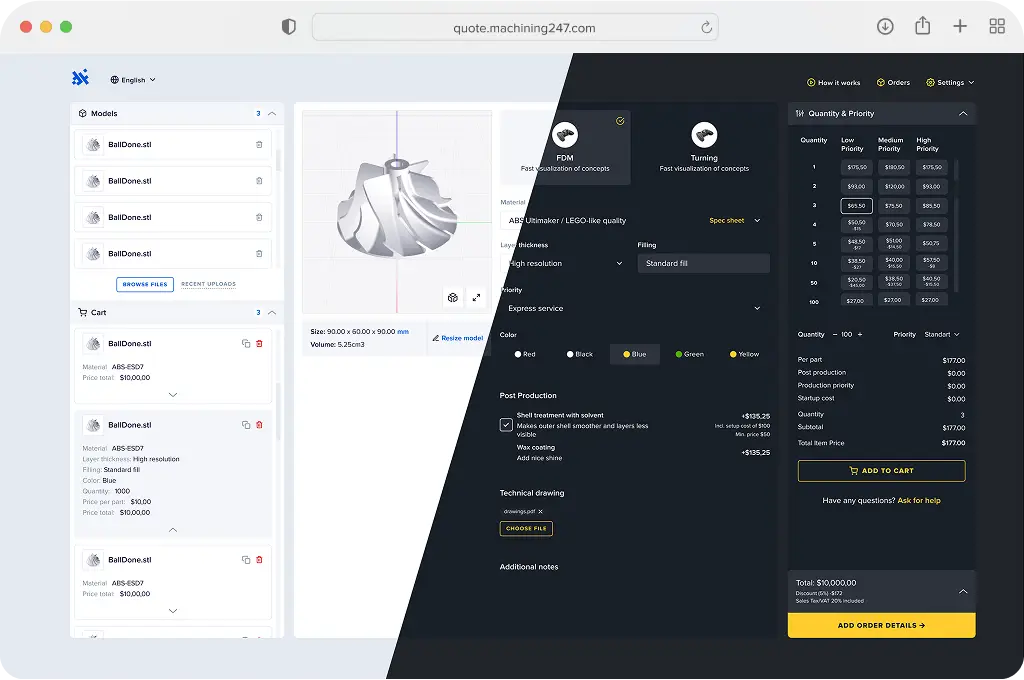