Tailor your workflow — your terms, your process.
DigiFabster’s Order Status Customization feature gives you full control over the naming of your production stages, so your digital workflow mirrors your real-world operations. Whether you’re managing cnc machining, laser cutting, injection molding, or metal fabrication, your team can now work within a system that speaks your language.
Designed for fabrication shops, metal shops, custom machine shops, and other on-demand manufacturers, this feature helps simplify communication and streamline your production management.
🔧 What It Does
With Order Status Customization, you can:
- Rename any manufacturing status in your pipeline
- Reflect your real production flow with labels like:
- “Pre-Production Setup”
- “Material in Stock”
- “Machining in Progress”
- “Bending & Finishing”
- “Inspection & QA”
- “Ready for Dispatch”
- Improve internal clarity in:
- Order tracking
- Job scheduling
- Manufacturing estimating
- Request-for-quote (RFQ) workflows
- Apply changes across your:
- Order Management Panel
- Line Item View
- Kanban board
- Packing list and production traveler documents
This creates a seamless link between your digital tools and your real-life manufacturing workflow.
🏭 Problems This Solves
Problem: Default workflow stages don’t match your shop’s process
✅ Solution: Rename statuses to reflect your internal language and real manufacturing milestones.
Problem: Hard to adapt software to your existing SOPs
✅ Solution: Align order statuses with your actual job shop procedures, whether you’re tracking metal parts, sheet metal, or 3D printed prototypes.
🚀 How It Works
- Go to Settings → Administration
- Select a status from your current workflow
- Rename it to fit your shop’s terminology (e.g., “Roughing Complete” or “Ready for QA”)
- Save — the new label appears across all panels, views, and documents
💡 Pro Tip
Use custom statuses to represent critical checkpoints in multi-axis machining, metal bending, powder coating, or engraving workflows. It’s a simple but powerful way to improve production tracking, ensure consistency across teams, and tighten up your manufacturing automation pipeline.
YOUR PATH FORWARD STARTS TODAY
Start your free trial now. No sales call required.
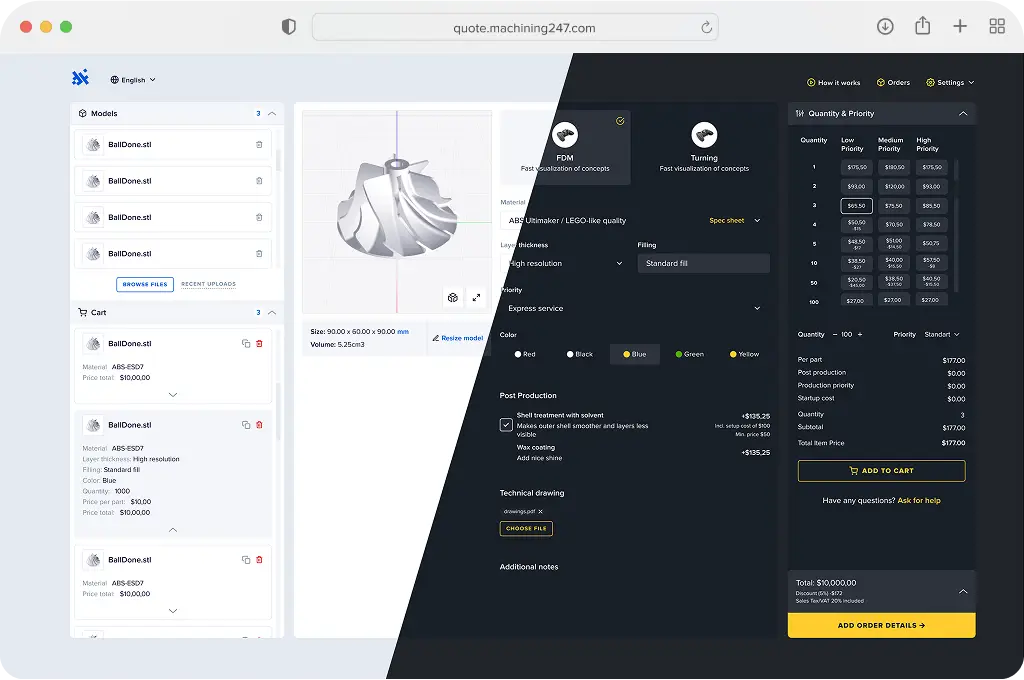